از آنجایی که پودر نانو آلومینیوم (NAP) می تواند عملکرد انفجار مواد منفجره حاوی آلومینیوم را بهبود بخشد، مواد منفجره بیشتری با NAP به عنوان عنصر فلز مورد مطالعه قرار گرفته است. اعتقاد بر این است که حساسیت مکانیکی مواد منفجره را می توان با افزودن پودر آلومینیوم در اندازه نانو به طور قابل توجهی افزایش داد. با این حال، مکانیسم افزایش روشن نشده است.
به منظور روشن کردن اثرات NAP بر حساسیت مکانیکی مواد منفجره، دو ماده منفجره حاوی آلومینیوم مبتنی بر RDX با نسبت وزنی و فرآیند آمادهسازی یکسان با وجود پودرهای آلومینیوم با اندازههای نانو و میکرون متفاوت مورد بررسی قرار گرفت. مورفولوژی و نسبت اتمی سطح دو ماده منفجره با میکروسکوپ الکترونی روبشی با آزمایشهای طیفسنجی پراکنده انرژی مورد بررسی قرار گرفت. زاویه تماس و سایر خواص ریزساختاری مواد منفجره توسط نرم افزار Material Studio محاسبه شد. نتایج نشان داد که فعالیت ضربه و اصطکاک توسط اندازه ذرات آلومینیوم و اجزای انفجاری تعیین میشود. این مقاله مکانیسم افزایش حساسیت مواد منفجره را با افزودن NAP، که مرجعی برای طراحی علمی و فنی مواد منفجره جدید است، روشن کرد.
برای مواد منفجره آلومینیومی، پودر آلومینیوم می تواند مقدار زیادی گرمای واکنش را در واکنش ثانویه پس از موج انفجار آزاد کند که باعث افزایش گرمای انفجار و حجم ویژه ماده منفجره در حین انفجار می شود و همچنین باعث می شود ماده منفجره ظرفیت کاری بالاتری داشته باشد .
به همین دلیل است که به آن مواد منفجره پرقدرت یا مواد منفجره قوی می گویند و به یکی از مقوله های اصلی تحقیقاتی در زمینه مواد منفجره تبدیل شده است. در مطالعه مکانیسم واکنش انفجار بین پودرهای آلومینیوم و مواد منفجره، نظریه واکنش ثانویه مواد منفجره حاوی آلومینیوم ارائه شده است:
پودر Al موجود در فرمولاسیون در واکنش در جبهه موج در طول انفجار شرکت نمی کند. برای واکنش آزادسازی انرژی در جبهه موج انفجار، پودر Al یک ماده گرماگیر بی اثر است که انرژی آزاد شده را توسط واکنش انفجاری از جبهه موج انفجار جذب می کند. در عین حال، پودر هدایت حرارتی خوبی دارد (ضریب هدایت حرارتی 230 W/(m·K-1) است).
با انبساط سریع محصولات انفجار، بخشی از انرژی در جبهه موج انفجار به سرعت به هوا منتقل می شود. این باعث میشود انرژی که از انتشار انفجار مواد منفجره پشتیبانی میکند، کاهش یابد، که از نظر ماکروسکوپی در کاهش فشار انفجار و سرعت انفجار مواد منفجره آلومینیومی با افزایش محتوای پودر Al منعکس میشود. به منظور بهبود ساختار خروجی انرژی انفجار مواد منفجره آلومینیومی، زمان شرکت پودر Al در واکنش انفجار پیشرفته است.
اندازه پودر آلومینیوم تأثیر قابل توجهی بر عملکرد انفجار مواد منفجره دارد. پودر آلومینیوم با اندازه کوچک بیشتر با محصولات انفجاری انفجاری با زمان واکنش پیشرفته، حجم واکنش زیاد و آزادسازی سریع انرژی واکنش نشان میدهد که ظرفیت کاری مواد منفجره را افزایش میدهد. به خصوص افزودن پودر آلومینیوم در اندازه نانو می تواند به طور موثر ظرفیت کاری مواد منفجره را بهبود بخشد.
دانشمندان نانو آلومینیوم و کاربردهای آنها را در پیشرانه های موشک مایع و جامد مورد مطالعه قرار دادند. مشخص شده است که مؤثرترین راه برای دستیابی به احتراق کامل، استفاده از پودر آلومینیوم با اندازه ذرات حداقل 1 تا 2 مرتبه کوچکتر از آنچه در پیشرانه های جامد معمولی استفاده می شود، است. از این رو تحقیقات در مورد کاربرد نانو پودر آلومینیوم در مواد منفجره در سال های اخیر توجه بیشتری را به خود جلب کرده است. برخی از محققان به طور سیستماتیک ویژگی های مواد منفجره مبتنی بر RDX، مانند حرارت انفجار ، سرعت انفجار ، توانایی شتاب فلز ، انرژی انفجار زیر آب ، اثر انحنای جلو و غیره را مطالعه کرده اند.
برخی از مقالات همچنین تأثیر نانو آل را بر حساسیت مواد منفجره مبتنی بر سیکلو تری متیلن تری نیترامین (RDX) گزارش کردند، که به وضوح نشان داد که افزودن نانو آل باعث افزایش حساسیت مکانیکی و حساسیت شعله ماده منفجره شد. با این حال، تحقیقات در این زمینه به اندازه کافی عمیق نیست. نتایج فقط عملکرد ماکروسکوپی مواد منفجره و برخی نظریه های اساسی را منعکس کردند. نقش ریزساختار بر عملکرد مواد و نظریه علمی مرتبط هنوز مشخص نشده است. تا به حال، مکانیسم NAP که باعث افزایش حساسیت مکانیکی و حساسیت شعله مواد منفجره می شود، درک نشده است. نتایج قبلی به اندازه کافی در مورد بهبود و طراحی فرمولاسیون مواد منفجره حاوی نانو Al ارائه نشده است.
کاهش حساسیت مکانیکی مواد منفجره هنوز یک راه بسیار موثر برای بهبود ایمنی ذاتی تولید، حمل و نقل، ذخیره سازی و سایر لینک های تولید مواد منفجره است. تحقیق در مورد عوامل موثر بر حساسیت مکانیکی مواد منفجره می تواند راهنمایی هایی برای بهبود عملکرد مواد منفجره از جنبه های طراحی فرمولاسیون مواد منفجره، پیش تصفیه مواد، فرآیند ساخت و غیره ارائه دهد.
برای آشکار کردن بیشتر تأثیر NAP بر حساسیت مکانیکی مواد منفجره، مواد منفجره مبتنی بر RDX با نسبت اجزای یکسان حاوی پودر آلومینیوم در اندازه نانو و میکرون با همان فرآیند به طور جداگانه تهیه شد. طیف انرژی اتمی سطح، زاویه تماس و سایر خواص مورد بررسی قرار گرفت. برای مدلسازی سازه و محاسبه پارامترهای سازه از نرم افزار Material Studio (MS) استفاده شد. همبستگی بین ساختار-فعالیت، اندازه پودرهای آلومینیوم، اجزای انفجاری و ضربه، حساسیت به اصطکاک روشن شد. نتایج این مقاله مرجع علمی برای کاربرد ایمنی نانو پودر آلومینیوم در مواد منفجره در آینده است.
در همين رابطه بخوانيد: بررسی واکنش پذیری پودر روی و پودر آلومینیوم
آزمایش و محاسبه
معرف ها و ابزار
پودر نانو آلومینیوم با خلوص 99.8 درصد با اندازه متوسط ذرات 100 نانومتر ساخته شده و ابزار حساسیت اصطکاک و ضربه (H3.5-10W) برای بررسی حساسیت مواد منفجره استفاده شد. یک میکروسکوپ الکترونی روبشی گسیل میدانی FEI QUANTA 600 (FE-SEM) که توسط FEI Co. USA ساخته شده بود برای بررسی مورفولوژی مواد منفجره استفاده شد. ولتاژ شتاب 10 کیلو ولت بود و آزمایشات در حالت خلاء بالا انجام شد. اندازهگیریهای جذب-واجذ N2 در 77 K با استفاده از سیستم جذب گاز Quantachrome Autosorb برای تعیین سطح ویژه نانو آل، میکرو آل و RDX بهطور جداگانه انجام شد. سطح ویژه نانو آل، میکرون آل و RDX 22.22، 0.55 و 0.344 m2/g است. آزمایشهای میکروسکوپ الکترونی عبوری (TEM) نانوآل با استفاده از هیتاچی (H 9000 NAR) انجام شد.
آماده سازی مواد منفجره
مواد منفجره مبتنی بر RDX حاوی پودرهای میکرون آلومینیوم و نانو آلومینیوم به ترتیب طراحی شده است. مورفولوژی پودر نانو آل و میکرون آل در شکل 1 نشان داده شده است. بنابراین، میکرون-Al یک رنگ خاکستری را نشان می دهد. شکل 1C نتایج آزمون TEM پودر نانو آل را نشان می دهد که به وضوح نشان می دهد که نانو آل در ساختارهای توپ مانند است. قطر نانو Al نیز مورد بررسی قرار گرفته و نتایج در شکل 1D نشان داده شده است. به وضوح نشان داده شده است که قطر پودر نانو آل در محدوده وسیعی قرار دارد، علیرغم اینکه قطر اصلی آن حدود 150 نانومتر است.
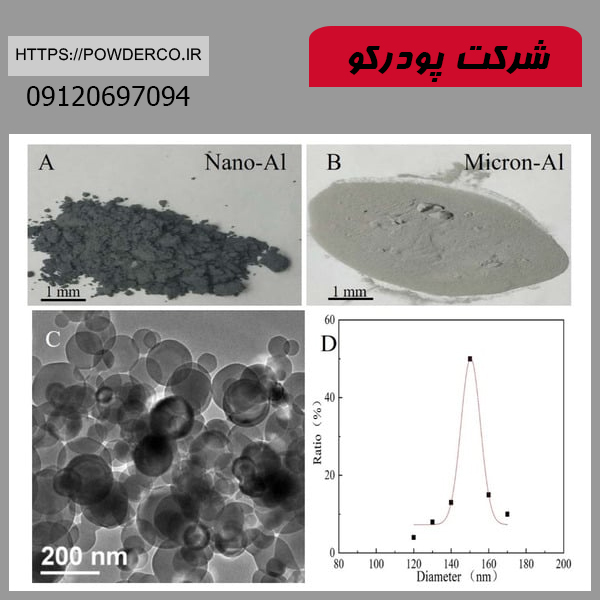
Figure 1. Photography of nano-Al (A) and micron-Al (B) powders. (C) TEM tests of nano-Al and (D) the distribution of the diameter of nano-Al powder.
مواد منفجره 1 و 2 با همین فرآیند تهیه شدند: موم پارافین توسط نفت اتر حل شد و سپس پودرهای RDX و آلومینیوم به ترتیب اضافه شدند. تمام معرف ها به مدت 30 دقیقه در خمیر گیر مخلوط شدند. سپس مخلوط ریخته شد و حلال تبخیر شد تا ماده منفجره به حالت نیمه خشک برسد، به این معنی که دیگر اتر نفتی وجود ندارد که بتوان آن را تبخیر کرد، اما حالت هنوز کمی مرطوب به نظر می رسد. مواد منفجره به دست آمده با توری 8 مش غربال و دانه بندی شد. پودرهای قالب گیری انفجاری به دست آمده در نهایت به طور کامل خشک شدند و برای بررسی عملکرد استفاده شدند. مورفولوژی عکس دو ماده منفجره در شکل 2 نشان داده شده است. شکل 2 نشان می دهد که ماده منفجره 1 با نانو آلیاژ رنگ عمیق تری در مقایسه با ماده منفجره با میکرون-Al نشان می دهد.
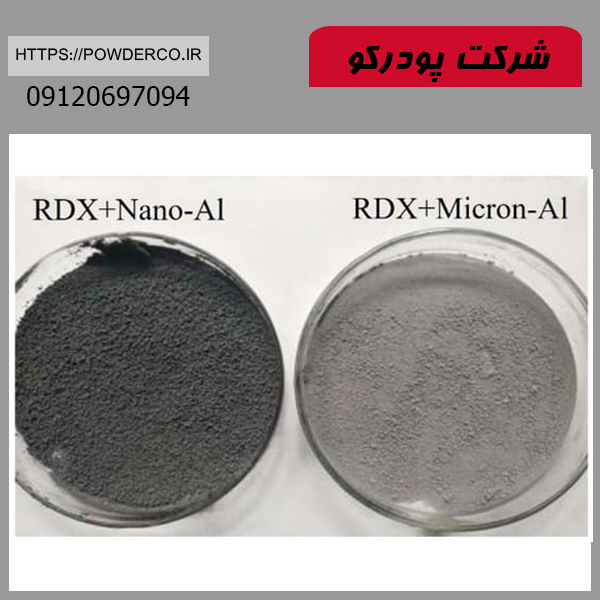
Figure 2. Photography of RDX with Nano-Al and Micron-Al.
آزمون عملکرد
تست حساسیت ضربه
حساسیت ضربه مواد منفجره توسط ابزار سنجش حساسیت ضربه چکش قطره H3.5-10W کالیبره شده اندازه گیری می شود. وزن چکش قطره ای 10 کیلوگرم و وزن ماده منفجره 50 میلی گرم است. معاینه با توجه به ارتفاع سقوط هر آزمون انجام شد. اعتقاد بر این است که 50 درصد ارتفاع افت آزمایشها حساسیت ضربه است. آزمون ها به دو گروه تقسیم می شوند و هر گروه 25 نوبت دارد. علاوه بر این، نتیجه نهایی مقدار زوج تمام دورهای آزمون در هر گروه است.
تست حساسیت اصطکاک
حساسیت اصطکاک مواد منفجره با فشار سطحی 3.92 مگاپاسکال با زاویه نوسان 90 درجه با وزن 50 میلی گرم تعیین می شود. آزمون ها نیز به دو گروه با 25 نوبت در هر گروه تقسیم می شوند. مقدار متوسط هر گروه به دست می آید.
انتخاب ساختار اولیه و محاسبه بهینه سازی اجزای انفجاری :
RDX
RDX یک کریستال مولکولی است. کریستال برش داده شد و یک لایه خلاء 20 Å به طور مستقیم برای محاسبه با استفاده از بسته شبیهسازی اولیه آب وین (VASP)، همراه با مجموعههای پایه موج صفحه اضافه شد. انرژی قطع موج صفحه اتخاذ شده در محاسبه 520 eV است. خود سازگاری الکترونیکی و معیارهای همگرایی نیروی بین اتم ها دقت پیش فرض VASP را اتخاذ می کند. در همین حال، اتم های نیمه پایینی در جای خود نگه داشته می شوند و اتم های نیمه بالایی بهینه می شوند. تمام عملیات روی ناحیه بریلوین سلولهای اولیه از یک شبکه نقطه K Monhkorst-Pack 3×3×1 با محوریت Γ استفاده میکنند. نیروی واندروالس با روش DFT-D3 اصلاح می شود. تابع تبادل-همبستگی بین الکترون ها با استفاده از روش Perdew-Burke-Ernzerh (PBE)در تقریب گرادیان تعمیم یافته (GGA) محاسبه می شود. انرژی محاسبه شده 1043.3066 eV است.
Al2O3
محاسبه باα-Al2O3 : (R-3C) به عنوان ساختار اولیه آغاز می شود. انرژی هفت صفحه کریستالی (111)، (110)، (101)، (011)، (100)، (010) و (001) که با ضخامت های مختلف بریده شده اند، به ترتیب محاسبه می شود. در هنگام برش، چهار لایه اتم در لایه زیرین وجود دارد، یعنی در مجموع 40 اتم. محاسبه با استفاده از بسته نرم افزاری VASP همراه با روش مجموعه های پایه موج صفحه انجام می شود.
انرژی قطع موج صفحه مورد استفاده در محاسبه 520 eV و استاندارد همگرایی برای خودسازگاری الکترونیکی 10-6 eV است. ضخامت لایه خلاء در جهت عمودی 20 Å است. تمام عملیات در ناحیه بریلوین سلول های اولیه از یک شبکه نقطه K Monkorst-Pack با مرکزیت Γ استفاده می کنند. موقعیت اتم های دو لایه بالایی (دو لایه پایینی اتم ها در جای خود نگه داشته می شوند) به طور کامل بهینه شده بودند به طوری که نیروی بین اتم ها کمتر از 10-3 eV/Å باشد. در این مقاله، GGA-PBE برای محاسبه تابع همبستگی تبادل بین الکترون ها اعمال می شود. داده های خاص نتایج محاسبه شده در جدول 2 نشان داده شده است.
محاسبه انرژی مقاطع مختلف Al2O3.
بر اساس محاسبات، می توان نتیجه گرفت که کمترین انرژی در بین چندین صفحه در سه صفحه کریستالی (110)، (101) و (011) ظاهر می شود که تقریباً 293.38- eV است. با توجه به اینکه Al2O3 یک کریستال با تقارن بالا است، تفاوت زیادی بین صفحات کریستالی (110)، (101) و (011) وجود ندارد. بنابراین، نتایج بهینه شده با روش ششم برش برای صفحه کریستالی نسبتا رایج (110) به عنوان ساختار مرجع در طول جذب انتخاب میشود. بنابراین برای محاسبه انرژی جذب پارافین روی سطح (110) قرار می گیرد.
مولکول پارافین
ساختار اولیه مولکول پارافین به صورت دستی توسط نرم افزار Material Studio مطابق نمودار شماتیک ارائه شده ساخته شده است. علاوه بر این، ساختار با استفاده از بسته نرم افزاری VASP بهینه می شود. با توجه به اینکه جذب مولکول های پارافین روی سطح آلومینا (110) باید محاسبه شود، سلول باید گسترش یافته و با وضعیت واقعی منابع محاسباتی ترکیب شود. یک مولکول پارافین حاوی 10 اتم کربن برای شبیه سازی انتخاب شده است. نرم افزار محاسبه و شبه پتانسیل انتخاب شده همان است که برای پارافین و RDX انتخاب شده است. از آنجا که تنها یک مولکول جذب شده انتخاب می شود، تعامل بین مولکول ها در صورت بهینه سازی مولکول حذف می شود.
مولکولها در یک سلول مکعبی بزرگ (در امتداد مورب) قرار میگیرند و سلول منبسط میشود تا اطمینان حاصل شود که فاصله مولکولی حدود 15-20 Å است. به منظور حذف تعامل بین مولکول های مجاور، محاسبه سلولی (ISIF = 2) زمانی که ساختار بهینه شده است انجام می شود. برای محاسبات ناحیه بریلوین سازه، یک شبکه نقطه K از نوع Monhkorst-Pack 1 × 1 × 1 با مرکزیت Γ به تصویب رسید. علاوه بر این، نیروی وان دروالس با روش DFT-D3 تصحیح می شود و تابع تبادل-همبستگی بین الکترون ها با روش GGA-PBE محاسبه می شود. در نهایت، نشان داده شده است که انرژی به دست آمده پس از بهینه سازی -173.074 eV است.
مولکول Al2O3 + پارافین
به منظور حذف برهمکنشهای ناشی از شرایط دورهای بین مولکولهای پارافین، سلولهایی برای انبساط زمانی انتخاب میشوند که مولکولهای پارافین روی سطح آلومینا جذب شوند. ساختار اولیه و بهینه مولکول های جذب شده پس از انبساط در شکل 3 (672 اتم) نشان داده شده است. نمای بالای ساختار نشان می دهد که ساختار مولکولی موم پارافین بر روی سطح آلومینا جذب شده است. ساختار اصلی شکل 3 ساختار اصلی را نشان می دهد و ساختار بهینه شده شکل 3 ساختار بهینه شده را نشان می دهد.
در محاسبات، دو لایه روی سطح آلومینا بهینه شده و دو لایه زیر ثابت میشوند. مولکول های پارافین کاملاً بهینه شده اند. در ساختار اولیه، فاصله عمودی بین مولکول های پارافین و سطح آلومینا حدود 0.5 Å است. پس از بهینه سازی، یک اثر دافعه بین دو ساختار نسبت به ساختار اولیه ایجاد می شود. در این شرایط، فاصله بین دو مولکول در حدود 2.4 Å است که در شکل 3 نشان داده شده است. انرژی ساختار بهینه شده 4950.088-eV است.
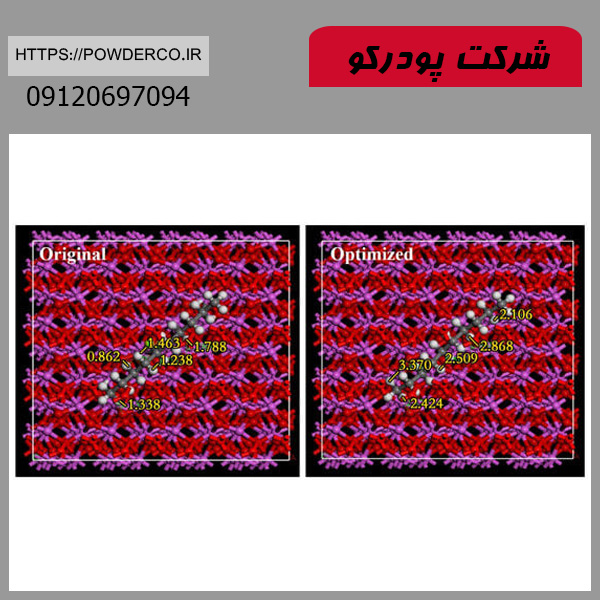
Figure 3.
Original and optimized molecular structure of paraffin adsorbed on Al2O3.
مطالعه مقاله واکنش پذیری پودر آلومینیوم و پودر منیزیم ؟ را از دست ندهید.
نتایج و بحث
مورفولوژی میکروسکوپی و نسبت عنصری سطح مواد منفجره
نتایج آزمایش مورفولوژی و طیف پراکنده انرژی (EDS) دو ماده منفجره در شکل 4/جدول 3 و شکل 5/جدول 4 به طور جداگانه نشان داده شده است. ترکیب عنصری دو ماده منفجره هم از نظر وزن و هم درصد اتمی نرمال شده است
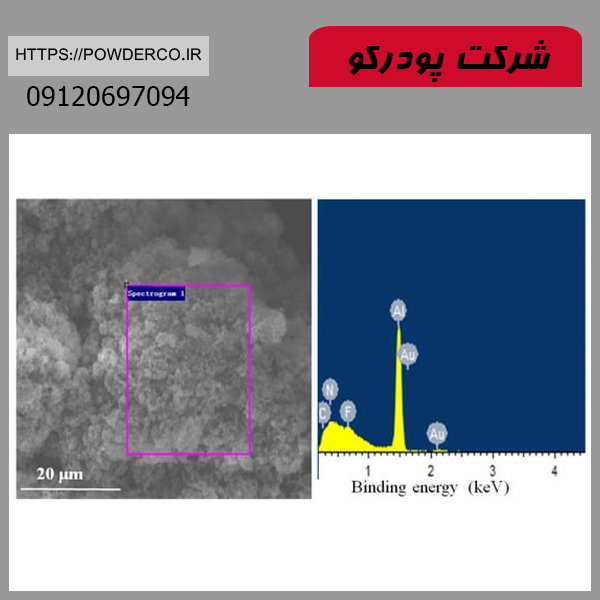
Figure 4. SEM image and EDS spectra of explosive 1.
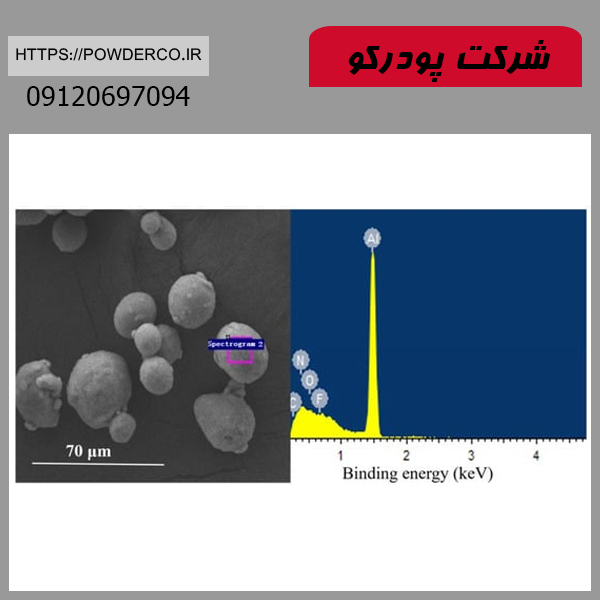
Figure 5. SEM image and EDS spectra of explosive 2.
مقایسه نشان داد که نسبت اجزای Al در دو ماده منفجره با یکدیگر متفاوت است، علیرغم اینکه نسبت وزن اولیه Al در دو ماده منفجره یکسان است. این را باید به دلیل توزیع اندازه متفاوت دو ماده منفجره نسبت داد. مساحت سطح ویژه NAP در ماده منفجره 1 104 برابر بیشتر از سطح میکرون Al در ماده منفجره 2 است. اگرچه، از نظر تئوری، محتوای Al در ماده منفجره 1 باید بیشتر از ماده منفجره 2 باشد، اما نتایج آزمایش واقعی کاملاً متفاوت است. نتایج محاسبات نظری این پدیده باید از تجمع جدی نانو آل در ماده منفجره 1 نشات گرفته باشد. نتایج آزمایش SEM مواد منفجره 1 و 2 به ترتیب در شکل 6 و شکل 7 نشان داده شده است. شکل 6 آشکارا نشان داد که نانو آل در ماده منفجره 1 به طور یکنواخت پراکنده نشده است.
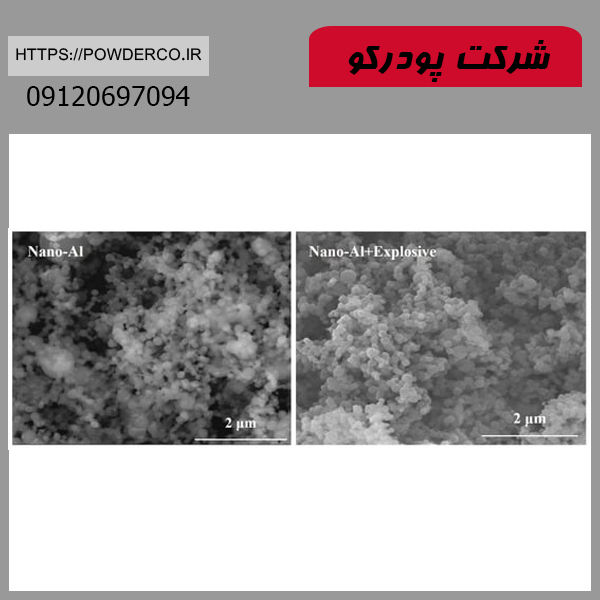
Figure 6. SEM images of nano-Al and explosive containing nano-Al.
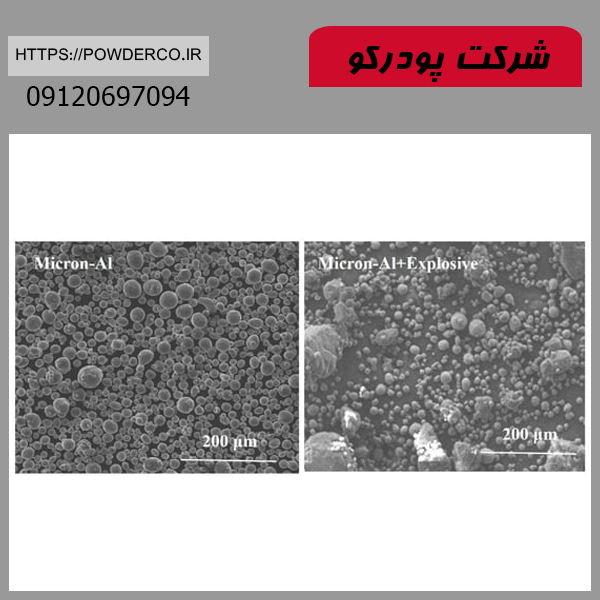
Figure 7. SEM images of micron-Al and explosive containing micron-Al.
تست های EM میکرون آل و ماده منفجره 2 در شکل 7 ارائه شده است.
مقایسه شکل 6 و شکل 7 نشان داد که قطر نانو Al بسیار کوچکتر از میکرون-Al است علیرغم اینکه هر دو مورفولوژی کروی کاملی را نشان می دهند. از سوی دیگر، همچنین به وضوح نشان داده شده است که تجمع نانوآل جدی تر از میکرون آل است. پراکندگی نانو آل در RDX نیز تحت تأثیر تجمع نانوآل است. میکرون-Al به طور یکنواخت تر از نانو-Al پراکنده شد.
تست و آنالیز انرژی سطحی و کار چسبندگی مواد
برای بررسی بیشتر ویژگیهای سطحی بین نانو آل/میکرون-آل، RDX و موم پارافین، چهار معرف با روش پروب آزمایش میشوند. نتایج به دست آمده در جدول 5 آمده است.
در دو نوع مواد منفجره، موم پارافین عمدتاً نقش حساسیت زدا را ایفا می کند. اگرچه مقدار موم پارافین بسیار کم است، اما موم پارافین را می توان با روش های آماده سازی مناسب به طور یکنواخت روی سطح ذرات انفجاری پوشانده و اثر کاهش حساسیت مکانیکی مواد منفجره را القا کرد [32].
کار چسبندگی بین موم پارافین و سایر اجزا را می توان با استفاده از انرژی سطحی هر جزء که در جدول 5 فهرست شده است محاسبه کرد. کار چسبندگی به عنوان کار ترمودینامیکی برگشت پذیر مورد نیاز برای جدا کردن سطح مشترک از حالت تعادل دو فاز تعریف می شود. فاصله بی نهایت هنگامی که دو فاز جدا شده یکسان باشند، به آن کار انسجام می گویند. کار چسبندگی و کار چسبندگی قوی ترین پارامترها برای نشان دادن تعامل بین دو فاز هستند.
با توجه به این مفهوم، عبارات ترمودینامیکی کار پیوند WAB و کار پیوستگی WCA برای مواد A و B را می توان به دست آورد:
WAB = γA + γB – γAB
(1)
WAC = 2γA
(2)
که γA و γB به ترتیب انرژی های آزاد سطحی دو ماده هستند و γAB انرژی آزاد سطحی آنهاست. علاوه بر این، با توجه به مفاهیم کار چسبندگی و کار چسبندگی، کاهش انرژی آزاد گیبس در واحد سطح زمانی که دو فاز مجزا به یکدیگر نزدیک می شوند و یک رابط را تشکیل می دهند برابر با کار چسبندگی و کار چسبندگی است.
ΔGAB = -WAB
(3)
ΔGCA = -WCA
(4)
بنابراین، بر اساس نقطه ترمودینامیکی، می توان مشاهده کرد که افزایش کار چسبندگی، کشش سطحی بین دو فاز را افزایش می دهد. کشش سطحی را می توان با فرمول (5) [32] محاسبه کرد. میزان چسبندگی محاسبه شده موم پارافین با RDX و آلومینیوم های مختلف در جدول 6 ارائه شده است.
γAB = [(γAd) 1/2 – (γBd) 1/2] 2 + [(γAp) 1/2 – (γBp) 1/2] 2
با توجه به جدول 6، کار چسبندگی موم پارافین با نانو Al به وضوح بیشتر از موم پارافین با میکرون-Al است. نتایج نشان میدهد که موم پارافین به راحتی روی سطح نانو آلیاژ نسبت به میکرون آل پوشانده میشود. نتایج همچنین توسط انرژی سطحی Al در ماده منفجره 1 (نانو-Al) تأیید می شود، که ثابت می کند انرژی سطحی کمتر از انرژی سطحی در ماده منفجره 2 (micro-Al) است.
بررسی های بیشتر همچنین نشان می دهد که کار چسبندگی موم پارافین به نانو Al اساساً مانند موم پارافین-RDX است. از آنجایی که مساحت سطح ویژه نانوآل بسیار بزرگتر از RDX است، می توان استنباط کرد که در ماده منفجره 1، موم پارافین بیشتری روی سطح نانوآل پوشیده شده است. به طور مشابه، صحت استنتاج نیز با این نتیجه تأیید می شود که وزن و درصد اتمی کربن در ماده منفجره 1 بیشتر از ماده منفجره 2 است.
تجزیه و تحلیل انرژی جذب بین اجزای انفجاری
با محاسبه انرژی جذب اجزای اصلی مواد منفجره، انرژی متناظر بین اجزای جداگانه و اجزای ترکیبی به دست آمده و در جدول 7 نشان داده شده است. بر اساس نتایج جدول 7، انرژی جذب متناظر موم پارافین به پودر Al و RDX مختلف را می توان به دست آورد و نتایج در جدول 8 نشان داده شده است.
از انرژی جذب می توان دریافت که در سیستم انفجاری پودر RDX و Al، زمانی که اندازه ذرات پودر Al از میکرون به نانومتر کاهش می یابد، پارافین به احتمال زیاد بر روی سطح پودر Al جذب می شود که همراه با بزرگ شدن سطح ویژه. بیش از 104 بار بنابراین، در سیستم انفجاری حاوی نانو آل، موم پارافین عمدتاً روی سطح پودر نانوآل پوشیده میشود [33]. بنابراین، در سیستم انفجاری حاوی میکرون آل، موم پارافین عمدتاً روی سطح ماده منفجره اصلی RDX پوشانده می شود.
تست و تحلیل حساسیت ضربه و اصطکاک مواد منفجره
بر اساس اندازه گیری مورفولوژی، عناصر سطحی، انرژی سطحی مواد منفجره و محاسبه کار چسبندگی، مشاهده شد که یکنواختی اجزای ماده منفجره 1 با وجود یکسان بودن اجزای مواد منفجره 1 و 2 ضعیف است. حساسیت مکانیکی پایین نیاز اولیه برای استفاده از مواد منفجره مخلوط است. بنابراین، حساسیت مکانیکی مواد منفجره 1 و 2 بررسی شده و نتایج در جدول 9 نشان داده شده است. به عنوان مقایسه، حساسیت ضربه و اصطکاک RDX و RDX + پارافین واکس نیز ارائه شده است.
جدول 9 به وضوح نشان می دهد که حساسیت به ضربه پارافین واکس RDX+ بسیار نزدیک به RDX است، به این معنی که پارافین واکس و RDX سازگاری خوبی دارند. موم تقریباً هیچ تأثیری بر حساسیت RDX ندارد [34]. در مقایسه با موم پارافین RDX +، حساسیت به ضربه ماده منفجره 2 که از میکرون-Al تشکیل شده است در بین تمام مواد کمترین است. این را باید به میکرون آل نسبت داد که در اثر ضربه زدن به ماده منفجره 2 تغییر شکل نمی داد و تغییر شکل میکرون آل نمی توانست RDX را مشتعل کند، که در نهایت حساسیت ضربه انفجار 2 را کاهش داد.
از طرف دیگر، حساسیت ضربه ماده منفجره 1 بسیار بالاتر از ماده منفجره 2 است و RDX همراه با حساسیت اصطکاک نیز بسیار بالاتر از ماده منفجره 1 است. از آنجایی که مساحت سطح ویژه نانوآل بسیار بزرگتر از ذرات RDX است، موم پارافین بیشتری روی سطح نانوآل پوشانده شده است، به این معنی که مقدار ذرات RDX در ماده منفجره 1 با موم پارافین کمتری پوشیده شده است.
به ماده منفجره 2، با همان مقدار موم پارافین، micron-Al به طور یکنواخت تر روی سطح ذرات RDX چسبیده است. تحت ضربه چکش قطره ای، RDX توسط میکرون-Al روانکاری و بافر می شود که منجر به حساسیت ضربه متفاوت دو ماده منفجره می شود. از نظر حساسیت به اصطکاک، ماده منفجره 1 بالاتر از منفجره 2 است که باید توسط نانو Al ایجاد شود. نانو Al مساحت سطح ویژه بالاتری نسبت به میکرون-Al دارد که در اثر اصطکاک آسانتر مشتعل میشود. در مقایسه با موم پارافین RDX و RDX +، حساسیت اصطکاک ماده منفجره 1 بیشتر از موم پارافین RDX + و RDX است که باید در اثر جذب موم پارافین بین نانو Al و RDX ایجاد شود.
بیشتر بخوانید : مقایسه پودر آلومینیوم و اکسید آلومینیوم (آلومینا)
نتیجه گیری
بر اساس بررسیهای ریزساختارها، اثر پوشش سطح-واسط و محاسبات مدلهای مولکولی مواد مواد منفجره مبتنی بر RDX حاوی پودر آلومینیوم در اندازههای نانو و میکرون، مشخص شد که تجمع در نانو Al با یک سطح ویژه بزرگتر در عین حال، بایندر فرمول مواد منفجره (به ویژه بایندر مبتنی بر پارافین) را می توان به راحتی روی سطح پودر نانو آلی پوشاند که حساسیت ضربه ای ماده منفجره را کاهش می دهد.
نتایج این مقاله روش ایمن تری برای طراحی مواد منفجره با کارایی بالا حاوی پودر نانو آل را ارائه می دهد. موم پارافین باید به راحتی روی ذرات RDX جذب شود و پوشش خوبی روی سطح RDX ایجاد کند. روشهای آمادهسازی جدید طراحی شده باید نحوه پوشش دادن پارافین را روی سطح ذرات مواد پرانرژی ابتدا در نظر بگیرند و سپس به طور یکنواخت آنها را با نانوآل مخلوط کنند.